Process Safety Management Program Guide
Frontline Data Solutions: Safety Simplified
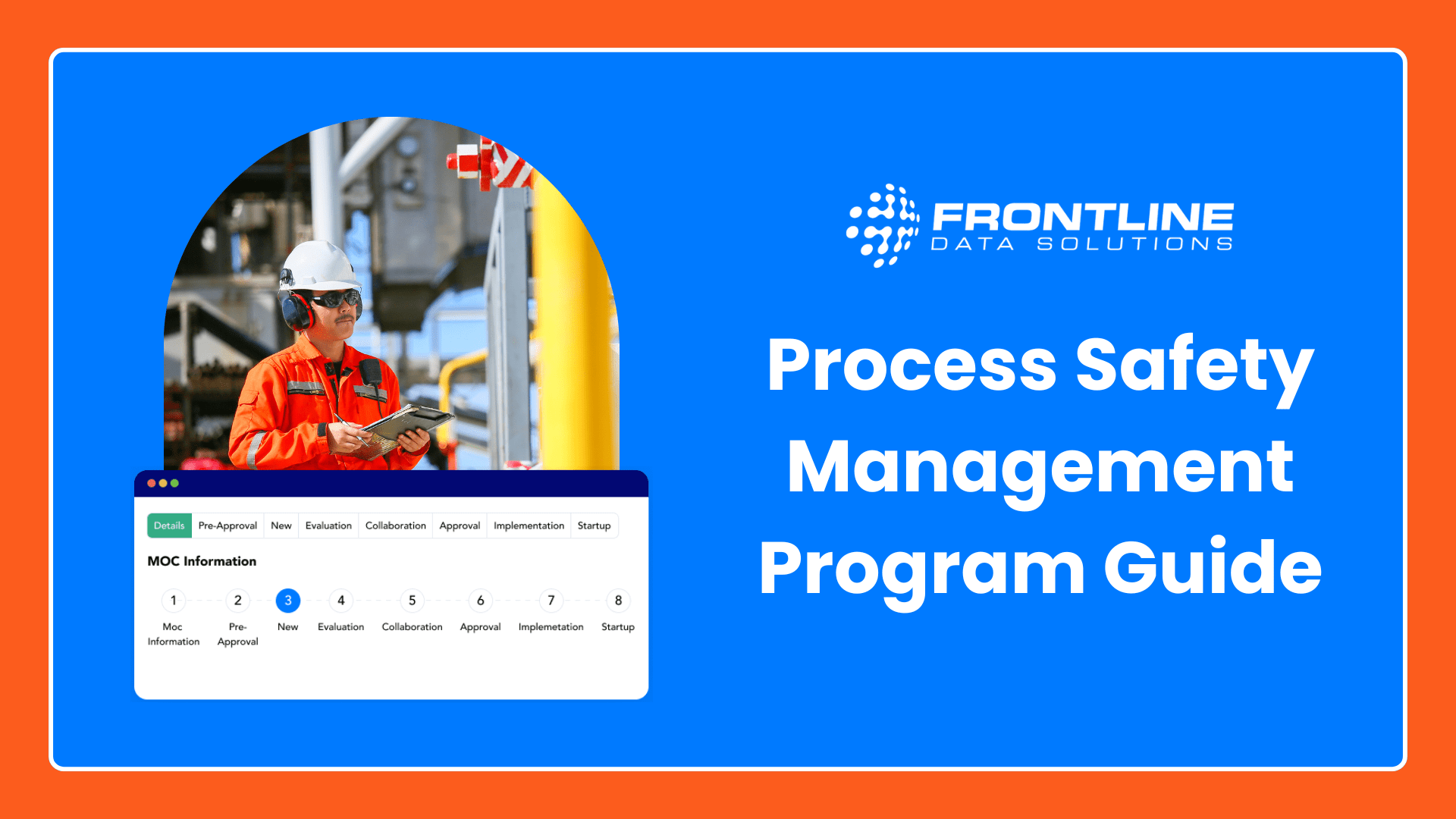
Chapter 1: What Is a Process Safety Management Program?
A process safety management (PSM) program is a framework that prevents the unintentional release of highly hazardous chemicals. This is to stop catastrophic incidents like fires, explosions, or toxic exposures from happening. Aside from protecting workers, PSM keeps communities safe from process safety incidents.
OSHA’s PSM Standard
The foundation of PSM in the United States is OSHA standard 29 CFR 1910.119. It outlines 14 elements that you must implement when your processes involve highly hazardous chemicals in quantities above specified thresholds.
The goal of the standard is to proactively identify and mitigate the risks of chemical releases. You do this by embedding safety practices throughout the design, operation, and maintenance of your processes. If your facility is subject to this standard, you’re legally required to maintain a compliant PSM program and may face significant penalties for violations.
Occupational Safety vs. Process Safety
Occupational safety focuses on preventing injuries and incidents that affect individuals. Examples of these include slips, falls, equipment accidents, and more. Process safety, on the other hand, targets low-frequency, high-impact events that can affect entire facilities or communities.
Think of it this way: occupational safety aims to protect the person, while process safety aims to protect the operation. Both are essential to overall EHS management, but process safety requires a more system-wide, engineering-driven approach to managing risk.
Industries Covered by PSM
PSM applies to highly hazardous industries where large volumes of chemicals are stored, used, or processed. These include:
- Chemical manufacturing
- Petroleum refining and oil & gas processing
- Pharmaceutical production
- Food processing facilities using anhydrous ammonia refrigeration
- Paints, coatings, plastics, and resins
- Agricultural chemical producers
- Water and wastewater treatment facilities
Even some facilities that don’t specialize in chemical production may fall under PSM if they handle covered substances in quantities above the threshold limits.
Common PSM-Covered Chemicals
OSHA maintains a list of highly hazardous chemicals with specific threshold quantities that trigger the need for a PSM program. A few common examples include:
- Anhydrous Ammonia
- Hydrogen Sulfide
- Chlorine
- Hydrogen Fluoride
- Acetylene
- Formaldehyde
You need to calculate the quantity of each chemical in the list of highly hazardous chemicals to determine whether you’re required to have a PSM program. Even if the total exceeds the threshold limit temporarily, you still need a program in place.
Chapter 2: The 14 Elements of OSHA’s PSM Standard
There are 14 separate requirements in OSHA’s PSM standard. They make up the PSM program elements that you’ll need to have in place for compliance.
Process Safety Information (PSI)
Process safety information is the backbone of your entire PSM program. It requires written details on the chemicals, technology, and equipment used in your processes. Without it, other safety efforts lack proper context and accuracy.
It’s not enough to collect safety data sheets or OEM manuals. For true success, you’ll need organized, up-to-date, and accessible information to help your team fully understand the process hazards.
Process Hazard Analysis (PHA)
The next element, process hazard analysis (PHA) is a structured approach to identifying and evaluating risks. This element requires a methodical team review of your process using techniques like HAZOP analysis. A strong PHA informs smarter decisions and keeps your team ahead of preventable incidents.
Operating Procedures
Written operating procedures are another important requirement for a process safety management program. These procedures must clearly guide frontline workers through startup, normal operations, emergencies, and shutdown.
They should be consistent with your process safety information and frequently updated. Involving frontline workers in procedure development not only improves the content but also increases buy-in and compliance. Well-structured procedures help protect equipment, prevent releases, and reduce downtime.
Employee Participation
OSHA requires a formal plan to involve employees in PSM activities. This is about creating safety ownership at every level within the company. Involving employees in safety committees, PHAs, or procedure reviews builds a stronger safety culture and uncovers cost-saving ideas from those closest to the work.
Workforce Training
Employees involved in operating processes must receive thorough, ongoing training on procedures, safety hazards, and emergency response. The training must be documented and verifiable. While in-person training can be valuable, using learning management software like Frontline LMS helps streamline delivery, ensure consistency, and simplify recordkeeping.
Contractor Management
Contractor management is another major requirement for PSM programs. It requires you to vet contractors for safety performance, inform them of hazards, and control their access to process areas. Hiring safe contractors reduces incident risks and ensures better job execution. Plus, strong contractor safety management protects everyone on-site and limits company liability.
Pre-Startup Safety Review (PSSR)
Before introducing hazardous chemicals into a process, you must verify that secure systems, adequate training, and safe procedures are in place. A PSSR checklist process ensures that your team doesn’t miss anything while preventing costly startup failures or safety gaps.
Mechanical Integrity (MI)
Mechanical integrity focuses on the ongoing inspection, testing, and maintenance of critical process equipment like tanks, piping, valves, and emergency shutdown systems. Through these methods, you can prevent equipment failures and hazardous releases.
Effective mechanical integrity programs prevent downtime and lost production, which can be devastating to a company. They ensure that you design and install new equipment, so it operates properly and safely.
Hot Work Permits
Under PSM, any spark-producing activity in or near a process area requires a documented hot work permit. This permit system ensures that you have proper precautions in place before welding, cutting, or grinding anything. This reduces the potential for fires that can destroy equipment and jeopardize employee health, safety, and morale.
An effective hot work program includes fire suppression tools, trained fire watch personnel, and strong documentation practices. The best practice is to use EHS software to track hot work documentation and ensure compliance.
Management of Change (MOC)
One of the most critical requirements of a PSM program is management of change (MOC). It’s the process of carefully planning, implementing, and reviewing process changes that may adversely affect health and safety. Under PSM, any change to equipment, procedures, chemicals, or facilities (excluding “replacement in kind”) must go through a structured evaluation and approval process.
For most companies, there’s not enough manpower to maintain documents, which puts them at risk of noncompliance. Oftentimes, MOC is the most missed step because of what it takes to complete it. This is common with companies that use spreadsheets and paper to keep track of the changes their teams are making. That’s why management of change software has become a popular tool within PSM programs.
MOC software like Frontline MOC simplifies the compliance process, so it’s easier to track and manage changes. With software, you can organize, sort, and review changes to gain more control and visibility over your process.
Incident Investigation
OSHA requires an investigation into any incident or near miss that could have resulted in a catastrophic release. The goal isn’t to assign blame, but to understand root causes and prevent future occurrences.
You should complete incident investigations immediately to ensure the accuracy of your findings. This involves collecting evidence, having witnesses write incident statements, and determining the root cause. Once you do that, it’s important to take corrective action and document your efforts. You can do this with incident management software, so the information is accessible if you need it for a regulatory audit.
Emergency Planning and Response
Even with the best systems in place, emergencies can happen. Your process safety management program must include clear response plans and employee training to minimize harm when incidents occur. This includes drills, evacuation plans, and coordination with local emergency services.
Strong emergency readiness reduces the scope and severity of incidents and builds confidence across your workforce.
Compliance Audits
To verify the effectiveness of your PSM program, OSHA requires audits at least every three years. These reviews assess whether your documented procedures are being followed and whether improvements are needed. While audits may disrupt operations temporarily, they’re crucial for identifying gaps and avoiding larger failures.
Trade Secrets
OSHA allows employers to protect proprietary information, but it must still be disclosed as needed to ensure safe operations and compliance. That means you must share relevant data with employees, contractors, or auditors even if you require NDAs. Transparency is critical to ensure that you base your safety decisions on accurate, complete information.
You can learn more about the PSM program elements in our blog post “The 14 Process Safety Management Elements.”
Chapter 3: Common Challenges in Building a PSM Program
Building and maintaining a compliant PSM program is a huge undertaking. The OSHA standard outlines clear requirements, but in the real world, meeting those expectations requires significant planning, coordination, and resources. Below are some of the most common challenges that your PSM program might face.
Keeping Process Safety Management Program Documentation Current
Process safety programs generate a mountain of documentation:
- Safety data sheets
- Operating procedures
- Inspection records
- Equipment specs
- Change logs
- Training documents
Keeping all this information up to date is critical not just for compliance, but also for day-to-day safety. A lack of accurate documentation increases the risk of operational errors, audit citations, and safety incidents.
Managing and Tracking Changes
Perhaps the biggest challenge PSM programs face is difficulty tracking changes. MOC is one of the most complex and critical requirements within the standard. Any changes to chemicals, processes, or equipment must go through a formal review and approval process. But this often turns into a bottleneck, especially when using spreadsheets or email chains to track approvals.
Bottlenecks in the MOC process can delay critical work, create compliance gaps, or even result in unapproved changes being implemented on the floor. The solution is to standardize and digitize your management of change workflow. A good MOC system provides visibility into every stage of the change process, with automated notifications and clear ownership for each step. That way, changes don’t fall through the cracks, and approvals happen faster.
Ensuring Employee Participation and Training Compliance
Another common challenge with PSM programs is getting consistent workforce engagement. This is especially true if you manage multiple shifts, departments, or locations. Oftentimes, employee participation drops because employers don’t effectively communicate the value of the PSM program. This can also happen if your PSM training isn’t specific to individual roles.
Training compliance is another issue teams face. Manual tracking of certifications and training dates often leads to missed renewals or inaccurate records. This affects compliance and creates unnecessary safety risks.
To improve participation and compliance, adopt training systems that automate assignments, track completion, and provide role-specific content. With training management software, for example, you can link training requirements directly to job tasks or MOC activities to reinforce safety at every level of your company.
Maintaining Audit Trails and Records for Inspections
Whether it’s for internal audits or regulatory inspections, maintaining clean, complete records is essential. OSHA expects you to retain documentation for several requirements. This includes incident investigations, PHAs, training records, and more. If your records are in paper files or stored across multiple systems, it’s incredibly difficult to pull together the right documentation during an audit.
Compliance red flags that regulators look for are:
- Missing records
- Unclear audit trails
- Inconsistent formatting
These increase your risk of citations or penalties. That’s why using safety compliance software is the best practice for PSM-regulated companies. With it, you can maintain permanent action logs, oversee approvals, and keep track of upcoming deadlines.
Chapter 4: Why MOC is Central to a PSM Program
Management of change is the heart of a successful process safety management program. Of all 14 elements of OSHA’s PSM standard, MOC is one of the most frequently cited for compliance violations. That’s because change is constant in industrial settings, and even minor modifications to processes, equipment, or personnel can introduce serious safety risks if unmanaged.
Common Challenges with MOC Compliance
Poorly executed MOC processes are a leading cause of serious incidents in high-hazard industries. Skipping or rushing change reviews can lead to unaccounted-for risks, incompatible equipment, invalidated safety assumptions, or failure to update operating procedures and training.
Some common MOC challenges you might encounter include:
- Unapproved or undocumented changes made under pressure
- Lack of clarity about what constitutes a change
- Inadequate communication between departments
- Paper or spreadsheet systems that make it easy to lose track of changes
- Missing documentation when auditors request records
These breakdowns increase the risk of accidents, regulatory citations, and legal consequences.
Chapter 5: How Frontline’s MOC Software Supports PSM Compliance
Management of change software is the number one tool you can use to simplify PSM compliance. It enables standardization across teams and locations to make sure everyone follows the same process. This solves the communication problem that you might face when coordinating large sitewide changes.
The other huge benefit of software is that it drastically reduces the amount of paperwork required to maintain compliance. Instead of updating spreadsheets, saving email threads, etc., you have all your notes, approvals, change logs, and more in a single location. When you need to review past changes or face a PSM program audit, you’re ready to go.
Frontline MOC is the gold standard for PSM compliance because it was built specifically around the PSM requirements. But it’s not just limited to the types of changes OSHA requires you to document. You can use it for other applications as well. Here are the ways that Frontline MOC simplifies safety compliance while improving efficiency.
Configurable Workflow Automation
When you manage changes with Frontline MOC, they all go through an automated process workflow. This ensures consistency and closes compliance gaps to prevent oversights. The steps in our MOC workflow include:
- Pre-Approval*
- New
- Evaluation*
- Collaboration*
- Approval
- Implementation
- Startup
- Completion
*Optional stage
In the workflow, you have the option to distinguish between PSM and non-PSM related changes. When you pull reports, you can filter by type to get quick access to all your compliance data.
This automated workflow ensures that every change follows a consistent sequence of review, approval, and implementation. This prevents your team from skipping steps, allowing you to route tasks to the right personnel at the right time. Built-in reminders and status tracking also help you avoid bottlenecks and overdue reviews.
Audit-Ready Process Safety Management Program Reports
One of the biggest headaches of the MOC requirement is compliance reporting. To have accurate reports, you need accurate data. And when you track everything manually, you’re bound to have missing information.
Within Frontline MOC, you can put together compliance reports within a few minutes. Filters allow you to pull only the data relevant to a specific time frame, department, facility, or even piece of equipment affected. You’ll have a record of all sorts of information, including:
- Who opened the MOC project and who approved it
- When different tasks were completed and who completed them
- Equipment affected by the change
- Attachments related to the change
- Names of everyone who worked on the MOC
This level of documentation solves many of the problems you might typically face with MOC compliance. Since the entire paper trail is digital, it protects your company from failing an audit and receiving fines.
Cross-Functional Collaboration
The optional collaboration stage in our Frontline MOC workflow is great for managing interdepartmental changes. It allows the MOC originator to add “collaborators” who can review the change online, ask questions, and provide comments. Most commonly, collaborators are subject matter experts or approvers who have deep knowledge of the process or business.
This stage encourages your team to provide detailed feedback before investing in an MOC project. Oftentimes, collaboration can save time and money by preventing you from exploring changes that don’t align with business goals. Plus, it provides even more documentation for compliance in case you do run into problems after implementing a change.
Version Control and Visibility
Manual systems often lack clarity on which document or procedure is the latest version. Frontline MOC software automatically updates your documentation and logs all changes as you complete them in real time.
You can use the MOC dashboard to view data points like:
- Number of MOCs completed
- Number of MOCs past due
- Count of PSM versus non-PSM MOCs
- MOCs awaiting approval
- Send notices awaiting signoff
It also allows you to break down MOCs by stage, priority, and more. Having access to these data insights keeps your leadership team in the loop and prevents miscommunication. They’re essential for running a compliant process safety management program that meets the MOC requirements.
How NCTI Reached Its Process Safety Goals with EHS Software
Nippon Chemical Texas Incorporated (NCTI) used EHS software from Frontline Data Solutions to increase visibility, improve compliance, and simplify their approach to process safety.
Chapter 6: PSM Program Best Practices
Once you get your process safety management program in place, the hard part is maintaining it. Because there are so many requirements, it’s not uncommon for teams to fall behind with compliance. If you follow these best practices, though, it should remove some of the burden of keeping up.
Start with a Clear Implementation Plan
If you haven’t already implemented your PSM program, start by creating an implementation plan. This plan should cover the scope of the rollout and answer questions like:
- Which departments or processes will be affected by the PSM program?
- Which product lines or equipment should we track for compliance?
- Which employees will oversee the PSM program?
- What is our timeline for implementing the program across the site/company?
You should also include your strategy for meeting each of the 14 elements of the OSHA standard. Determine what you already have and what you need to do to reach full compliance.
It’s a good practice to break implementation into phases, so your team can focus on incremental progress. For example, prioritize foundational elements like management of change and process hazard analysis before rolling out supporting systems like training or contractor management. Document each step to create internal accountability and make future audits easier.
Secure Leadership Buy-In for Your Process Safety Management Program
Another key to success for your PSM program is buy-in from senior leadership. To do this, you have to explain the necessity of the program beyond compliance obligations. Getting buy-in before implementation ensures that you have the budget, resources, and attention you need to get the program off the ground.
This should be part of your broader efforts to improve safety culture from the top. Senior leaders can participate in the PSM program by asking questions about safety performance, joining audits and reviews, and celebrating safety milestones. Over time, these actions communicate the importance of your process safety efforts.
Conduct Regular Audits and Feedback Loops
The longevity of your PSM program depends on your ability to adapt and improve over time. That’s why recurring program audits and feedback loops are critical. Use compliance audits (OSHA requires them every three years) as an opportunity to evaluate the effectiveness of your processes, not just your documentation.
In addition to formal audits, informal feedback mechanisms empower your frontline workers to report issues, suggest improvements, and identify gaps. Anonymous suggestion boxes, regular toolbox talks, and digital comment forms can all help you find issues before they cause incidents.
If possible, include frontline employees in safety reviews and root cause investigations. Their insights are essential to understanding how procedures work in practice and where disconnects occur.
Leverage Data for Continuous Improvement
Finally, don’t forget the power of your data. It’s one of the most powerful tools you have for improving your process safety management program. Collecting, analyzing, and acting on data from incidents, audits, training records, and MOC reviews gives you a clearer picture of your program’s effectiveness.
For example, tracking metrics like overdue action items, repeat incidents, or audit findings by department can highlight where to focus your improvement efforts. Dashboards and reporting tools make it easier to visualize trends, share updates with leadership, and demonstrate compliance during inspections.
Data also helps ensure PSM document control, provides better traceability, and allows you to measure engagement (e.g., training completion rates or participation in hazard reviews). With this kind of transparency, you can make smarter decisions and keep your PSM program aligned with both regulatory and operational goals.
Want to Take Your PSM Program to the Next Level?
Book a personalized demo to explore how Frontline Data Solutions can help you increase PSM program compliance, effectively manage changes, and prevent process safety incidents.