Incident Investigation Process Guide for Risk Reduction
Frontline Data Solutions: Safety Simplified
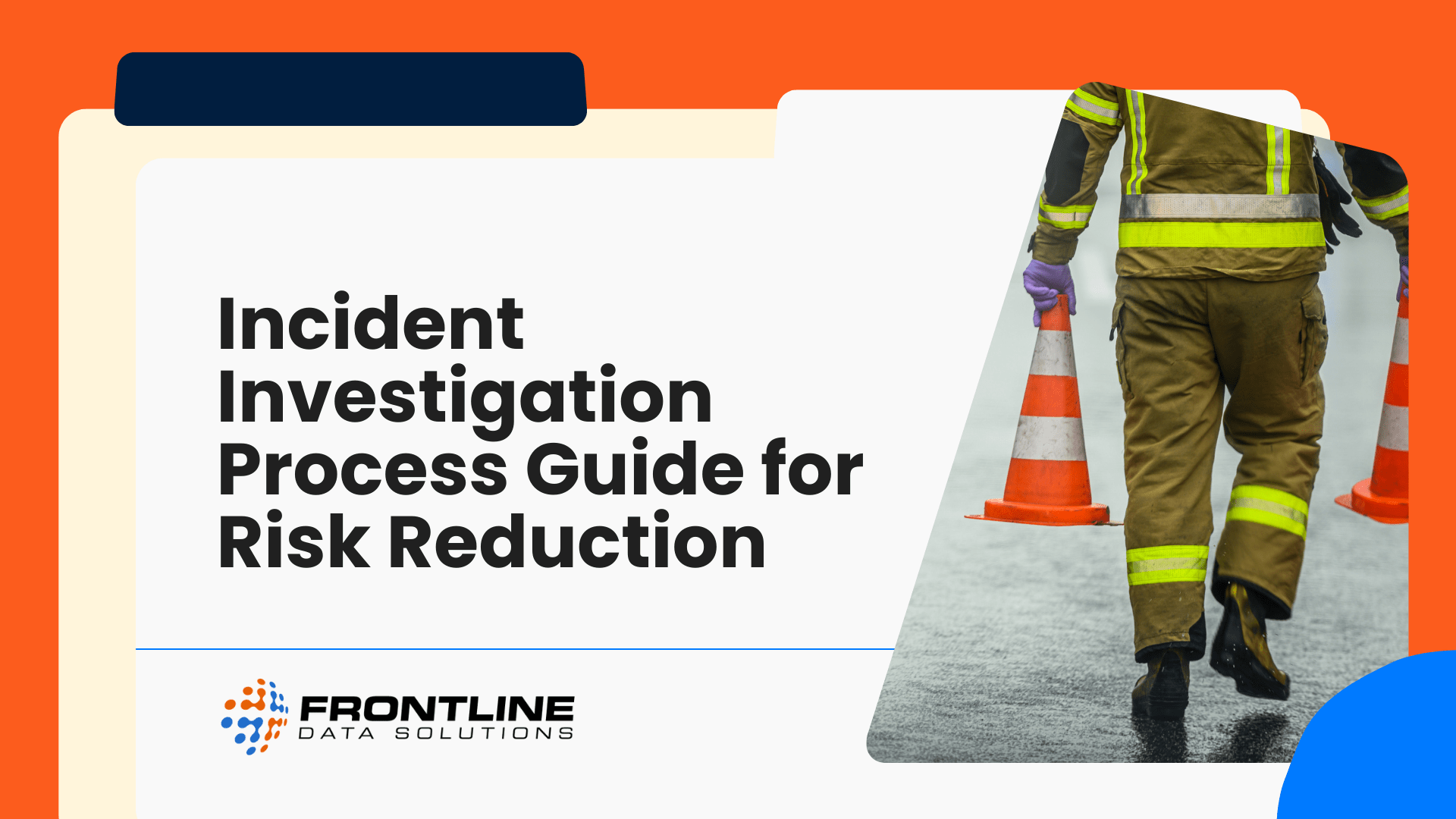
Time is of the essence when dealing with workplace incidents. Your EHS team needs to respond not only quickly but also effectively while meeting compliance requirements. The key to this is having a strong incident investigation process. Without it, you won’t be able to standardize your strategy, maintain compliance, and protect frontline workers.
For most teams, the challenge is that incidents are complex. They often require detailed documentation and collaboration across departments. Regulators like OSHA and the EPA expect you to maintain incident records that show evidence of corrective actions and hazard control measures. Any gaps in your process can lead to regulatory fines, legal issues, or recurring incidents.
This handbook covers the essentials of incident investigation, so you can implement a standard process across your company. Learn the best practices for investigating root causes, implementing corrective actions, and making lasting improvements to your processes, equipment, and more.
Chapter 1: Why Incident Investigation Matters
The purpose of the incident investigation process is to determine the cause of an incident and implement control measures that prevent it from happening again. This requires both detailed documentation and proactive follow-up.
Effective investigations have all kinds of benefits for your business, including:
- Improvement in key EHS performance metrics like injury rates, number of near misses reported, and hazards identified each month
- Higher employee engagement and satisfaction
- Lower unscheduled production downtime
- More effective hazard control measures
- Greater operational efficiency and productivity
- Reduced risk of compliance gaps, fines, and citations
Achieving these results, however, depends on whether you correctly identify the root cause of the problem. If you don’t, your incident investigation process won’t achieve more than checking compliance boxes.
For most teams, a thorough investigation serves as a learning opportunity. It shows that your company takes safety seriously. Better yet, it encourages workers to report hazards and build trust between managers and frontline workers. Over time, this feeds into your safety culture, making proactive risk management the new norm.
Regulatory Requirements to Know
In the United States, several OSHA standards mandate incident investigations. For example, OSHA standard 29 CFR 1904.33 requires you to maintain certain work-related injury and illness records for at least 5 years.
Under their process safety management standard, companies have to investigate incidents that “resulted in, or could reasonably have resulted in a catastrophic release of highly hazardous chemical in the workplace.” This standard also has requirements for the timing of the investigations.
Aside from OSHA regulations, your company might have to meet industry-specific standards. High-risk industries like oil and gas or chemical manufacturing often have requirements from the Environmental Protection Agency (EPA) or Bureau of Safety and Environmental Enforcement (BSEE) to follow.
Regardless of your specific requirements, most regulators require detailed, complete documentation as part of the incident investigation process. They also look for proof that you’ve taken corrective actions to try and prevent future incidents.
Chapter 2: The Incident Investigation Workflow
Standardization is the key effective incident investigation, the same as other compliance processes. Taking a consistent approach helps you find patterns over time, so you can continuously improve what you’re doing. Plus, it keeps your team organized, making them more successful at future incident prevention.
Aside from meeting compliance requirements, there’s no “best” way to investigate incidents. Your workflow will depend on the resources and people you have. Here are a few things you should consider when coming up with your process steps:
- What compliance requirements do we have to fulfill?
- How many people will be available to help conduct investigations?
- What technology (if any) will you use to document your process?
- What is your company’s expected completion timeline for investigations?
A good general outline for the incident investigation process is:
- Address immediate needs and secure the scene.
- Notify internal and external stakeholders.
- Collect evidence.
- Document the incident details.
- Identify the root cause(s).
- Develop corrective and preventive actions.
- Report and follow-up with your corrective actions.
If you’re just getting started, this is a great structure to follow.
Step 1: Address Immediate Needs and Secure the Scene
The priority after any incident is to make sure everyone is out of immediate danger to prevent further harm. If anyone has an injury, get them medical attention. Once you’ve done that, you need to secure the incident scene to preserve evidence. For example, you might need to turn off equipment or restrict access to the area. This ensures that the next steps go as smoothly as possible.
Step 2: Notify Internal and External Stakeholders
The next step is to notify internal and external stakeholders of what’s happening. Examples include plant managers, regional directors, and local emergency service providers. It all depends on the scope of the incident. For major incidents, it’s important to escalate the information quickly so you can get support. And depending on the industry you’re in, you might need to notify OSHA within a certain timeframe.
Step 3: Collect Evidence
When the scene is fresh, gather evidence quickly and make sure it’s accurate. Pictures, videos, security footage, etc., are just some of the types you can collect. You’ll also want to identify the people involved, so you can conduct witness interviews promptly. This prevents the details from becoming blurry or incorrect.
Step 4: Document the Incident Details
A critical step in the incident investigation process is documentation. This is where many teams struggle to meet compliance requirements. Compile a detailed record of the incident, making sure it answers questions like:
- What happened? When? Where?
- Who was involved?
- What were results of the incident?
- What were the conditions at the time of the incident?
Step 5: Identify the Root Causes
When you’ve collected all the data, the next step is to do a root cause analysis. Your goal is to figure out the deepest root cause(s) of the incident. The deeper you go, the better your corrective actions will be. Don’t make the mistake of falling back on generic root causes (e.g., inadequate training, human error, etc.). As you do your analysis, try to answer this question: “What system, procedure, or condition allowed the worker to make the unsafe decision that led to this incident?”
Step 6: Develop Corrective and Preventive Actions (CAPA)
Once you know the root cause(s), you can come up with meaningful action. Corrective actions address the immediate problem while preventive ones reduce the likelihood of recurrence. Part of this step is assigning actions and setting a deadline for completion.
Step 7: Report and Follow-Up with Corrective Actions
The last step of the incident investigation process is to finalize your report. It should include all the documents you’ve collected so far. Make sure you summarize the facts and your analysis in a way that makes the process and findings clear to anyone who reads the report.
Part of writing an incident report is following up with any action items you scheduled in the previous step. Using action tracking software is a great way to get quick visibility on the status of your investigation.
Following these steps will help your safety team conduct thorough and effective investigations. This is key if you want to make meaningful improvements rather than simply documenting past events.
Chapter 3: Root Cause Analysis in Practice
When investigating workplace incidents, root cause analysis (RCA) is one of the most critical steps. That’s because the effectiveness of your prevention measures depends on the quality of your RCA findings.
There are almost always several layers to an RCA. Oftentimes, as you go along, you’ll untangle a whole mess of contributing factors that influenced the outcome of the incident. Make sure you properly distinguish between these three key elements of your analysis:
Direct Cause: The immediate event or condition that led to the incident (e.g., an employee slipping on a wet floor).
Contributing Factors: Additional conditions or behaviors that made the incident more likely or more severe (e.g., inadequate signage, poor lighting, delayed cleanup).
Root Cause: The underlying, systemic issue that allowed the contributing factors to exist (e.g., absence of a formal housekeeping procedure or inadequate safety inspections).
Addressing only the direct cause tends to produce quick fixes that fail over time. Tackling the root cause, however, leads to lasting improvements.
Common RCA Methods
There are several methods you can use to conduct a root cause analysis. The most popular ones are:
The best method depends on the type of incident and the data you have. For example, fault tree analysis is great for complex or technical incidents. But it’s less straightforward and more time-consuming than a standard 5 why analysis. Choosing the right tool depends on the complexity of the incident, the availability of data, and the expertise of the investigation team.
Root Cause Analysis Examples
Here are a few examples of RCA to help you better understand its applications and uses.
Chemical Spill Prevention
A manufacturing facility experienced recurring small chemical leaks. After doing a 5 why analysis, the EHS team found out that the engineering team was replacing worn out valve seals with non-spec parts to save costs. To fix the problem, they updated the company’s procurement procedures to enforce OEM part use.
Forklift Collision Avoidance
A warehouse forklift driver collided with a support beam and broke their arm. Using a fishbone diagram, the EHS team uncovered several unsafe factors:
- Inadequate driver visibility around corners
- Cluttered warehouse aisles
- Poor traffic management
- Ineffective communication at the ends of aisles
With these findings, they installed endcap mirrors, revised PIT training, and built designated lanes to reduce incidents to zero over 12 months.
High-Pressure Line Failure
A line rupture at an oil and gas site prompted the safety team to conduct a fault tree analysis. They learned that an unapproved material change several months before the incident reduced the line’s tensile strength. To fix the issue, the EHS team implemented stricter management of change (MOC) procedures.
How NeoGraf Improved Visibility with Frontline ACT
NeoGraf used Frontline ACT to organize all its EHS data in one place, gaining more visibility and better overall performance in the process.
Chapter 4: Common Incident Investigation Mistakes
Without a good incident investigation process in place, it’s easy to make mistakes. Here are the most common ones that teams make. As you develop your process, find ways to avoid these issues if you want accurate findings and effective CAPA measures.
Rushing the Process
If your team feels pressure to get results quickly, they might cut corners to just get the investigation done. But rushing the process almost always leads to missed details, incomplete solutions, and repeat incidents. Always prioritize thoroughness over speed, especially when dealing with high-stakes events.
Focusing on Blame
Another common mistake is focusing corrective actions on blame. In general, blame-focused incident investigations create a culture of fear. They discourage frontline workers from reporting incidents. And that defeats the entire purpose of the investigation process—to understand events so you can prevent them from happening again. Consider adopting the principles of human and organizational performance within your safety approach.
Poor Documentation or Missing Evidence
After an incident happens, you have a limited window of opportunity to collect the details. The longer you wait, the more likely you are to miss critical insights in your investigation. You also want to practice good recordkeeping habits. Every investigation your team completes should provide a clear record of the steps you’ve taken to draw your conclusions.
Failure to Follow Up on Corrective Actions
Lastly, and most importantly, is the mistake of not monitoring your corrective actions. If you don’t review action items after implementation, how will you know they worked? Oftentimes, you’ll find that your solutions need revision over time to stay effective. That’s why it’s so important to assign action items, track them to completion, and set up recurring reviews to ensure their long-term success.
Chapter 5: Best Practices for Effective Investigations
If you do it right, an incident investigation can strengthen your entire safety program. Following these best practices is key for building an effective and efficient process that exceeds compliance requirements and leans into continuous improvement.
Involve Cross-Functional Teams in the Process
Your EHS department can’t solve every problem on its own. That’s why involving people from operations, maintenance, HR, and more creates a better outcome. Each role within your team provides a unique perspective to help make action items more effective. Plus, it also ensures complete buy-in to new solutions so that everyone stays in the loop.
Use Structured Methodologies for RCA
It’s very important to be intentional with your root cause analysis. Unstructured brainstorming is not an effective way to figure out the underlying issue of an incident. You need to lay out all the facts you have about the incident and come to a logical conclusion about why it happened. Lean on the methodologies outlined in chapter three as a best practice for RCA.
Standardize Evidence Collection and Documentation
Like RCA, you also need a standard process for documenting your incident investigation process. This includes not only your findings but also the steps you take to address them. Use predefined forms, incident management software, and standard workflows to organize your team. This increases consistency and reduces the risk of missed deadlines, details, and more.
Link Investigation Results to Broader Safety Initiatives
The incident investigation process holds much more value than documenting past events. It’s a great tool for learning more about the effectiveness of your entire EHS program, so you can make it better with each new insight.
The best way to maximize your findings is to apply them to all areas of your safety program. This includes training materials, safety meetings, hazard assessments, and more. Linking your findings to ongoing safety initiatives encourages continuous improvement. And if you want to build a proactive approach to safety, this is key.
Chapter 6: Documentation and Recordkeeping
Excellent documentation takes your incident investigation process to the next level. Without accurate records, you won’t be able to meet compliance requirements. But more than that, you also won’t learn as much from each incident. Here are some of the best practices for documenting injuries, illnesses, and more.
Required Forms and Reports for Compliance
You have to have all your required compliance forms organized and accessible. The exact forms depend on your industry, workforce size, and processes.
Beyond federal requirements like the OSHA 300, 301, and 300A forms, don’t forget about local regulations. State agencies and insurance companies may require other forms of documentation related to your incident investigations.
Make sure you keep these forms in a central location for managers to fill out when there’s an incident. Having a central repository also makes it easier to keep documents updated when requirements change.
Building an Investigation File
Another good practice is to have a separate file for each incident. This file should include information like:
- Incident report forms with date, time, and location
- Witness statements with contact information
- Photographs, diagrams, and video evidence
- Equipment inspection reports or maintenance logs
- Root cause analysis worksheets and findings
- Corrective and preventive action (CAPA) documentation
- Relevant communications or meeting notes
Organizing this information in a logical, chronological order makes it easy to review during audits or legal proceedings. Plus, it’ll be easier to identify patterns when analyzing incident trends over time. The better organized your data, the more useful it is in the future.
Digital Tools for Audit Readiness
Lastly, you should consider moving away from paper-based records and spreadsheets to document incident investigations. That’s because manual systems are more prone to errors and lost data. Not to mention, they’re more labor-intensive and less accessible in general.
Companies with the best incident investigation processes use EHS software to store their data. With software, everything’s in one location that’s easier to manage and update over time. This makes your process scalable to multiple locations, ensuring audit readiness across the company.
Chapter 7: How Frontline ACT Streamlines Incident Investigation
Frontline ACT is a user-friendly software tool for managing incidents and tracking action items. We’ve made it configurable, so you can track different types of incidents in a way that supports your existing workflows. With it you can bridge compliance gaps and boost visibility to improve your incident investigation process.
Centralized Incident Reporting
Switching to a digital system allows you to centralize your reporting process. With Frontline ACT, your team can complete reporting tasks and action items from their computer or phone. This gives you more flexibility while keeping the structure needed for compliant incident investigations.
Your team can upload photos, videos, and notes directly to the system. This means you have to track down all your report elements when you’re ready to compile them. Overall, Frontline ACT simplifies the reporting process so you can focus more on incident prevention.
Structured Investigation Workflows
Another major benefit of Frontline ACT is the configurable event workflow. Unlike competing software systems, we make it easy to set up specific steps for the different incidents or events you want to track.
For example, you can have separate event workflows for injury incidents, near misses, property damage, environmental accidents, and more. That way, you can tailor the software workflow to the required documentation and steps you want your team to follow.
Corrective Action Management
One of the biggest benefits of Frontline ACT is the action tracking capabilities. You can assign action items in real time throughout your incident investigation process and follow them to completion.
Automatic reminders and email notifications keep your leadership team informed of the team’s progress. And this visibility prevents the risk of oversight, ensuring more effective corrective actions in the long-term.
The built-in tracking system also keeps your team organized. When employees receive a new task to complete, it shows up on their dashboard so they can stay on top of their workloads. Over time, this improves employee productivity and satisfaction, potentially reducing turnover and lost time.
Audit-Ready Documentation
Within the Frontline ACT reporting tool, you’re able to build custom reports or use the standard ones available. Our user-friendly filtering and exporting capabilities make it easy to report on the status of incident investigations accurately and quickly.
When auditors or senior leaders need information about an incident, you’ll have immediate access to it. With that level of access, you’ll spend less time worrying about compliance and more time controlling risks.
Cross-Functional Collaboration
Depending on the type of incident, you might have several departments participating in the incident investigation process. Frontline ACT makes collaboration across departments easier by allowing individuals to work directly in the system.
The collaboration stage within our workflow allows your team leader to add people within your company as “collaborators” to a specific investigation. Once they select collaborators, they can start assigning action items that need to be completed.
With this flexibility, you’re not limited to documenting only the tasks your safety team is doing. Instead, you can capture all the work, regardless of who’s doing it, for greater visibility. The collaboration stage also gives everyone the chance to provide comments and feedback on proposed control measures before they move on to the implementation stage. That’s how Frontline ACT ensures that you make informed decisions at all stages of the incident investigation process.
Ready to See How It Works?
Book a personalized demo with our team to explore how Frontline Data Solutions can help streamline your incident investigation process.