PSM in oil and gas emphasizes the management of hazards associated with highly hazardous chemicals. It also establishes a comprehensive program for integrating technologies, procedures, and management practices.
From 2016 to 2020, there were 386 fatal injuries in the private sector of the oil and gas industry. PSM aims to reduce the likelihood of these fatalities through careful planning, execution, and oversight of operational hazards and process changes.
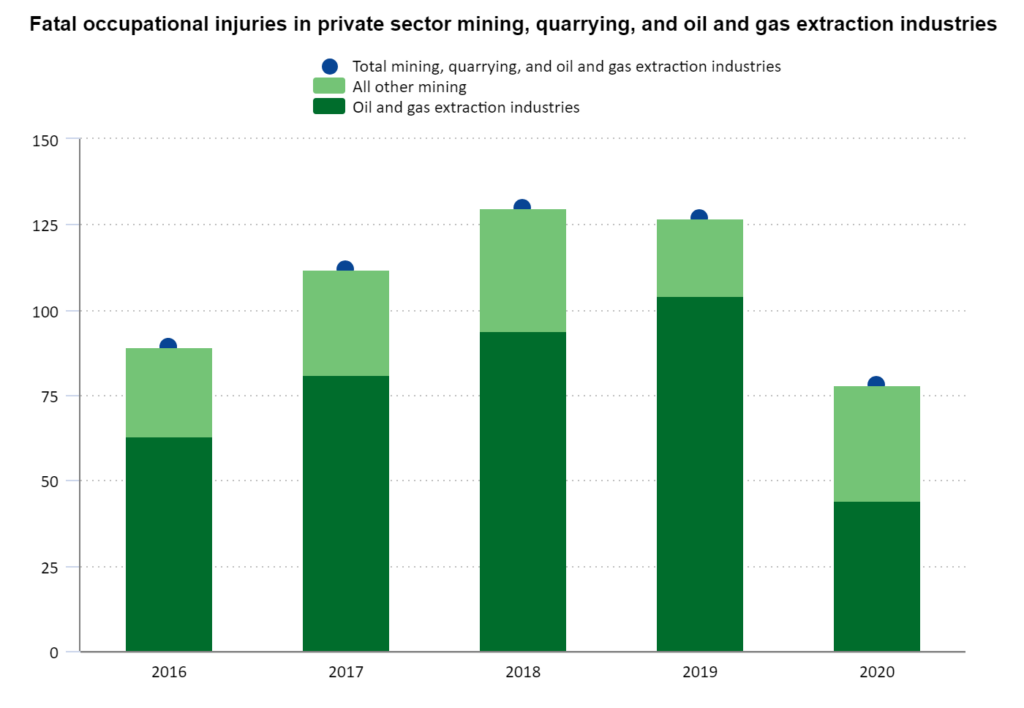
Several types of processes in the oil and gas industry have the potential for chemical releases that create dangerous fire, safety, and health hazards. One example of this is the process of refining petroleum into fuel.
Petroleum refining begins with the distillation, or fractionation, of crude oils into separate hydrocarbon groups. These groups are then converted into more useful products. Through cracking, reforming, and other conversion processes, refineries remove impurities to improve product quality.
No matter how routine this process may be, it still poses a variety of safety hazards to the workers involved in it. If you work in the production of oil and gas, these are some potential process safety management issues you need to be aware of.
Crude oil pretreatment (desalting)
As a first step in the refining process, contaminants such as water, inorganic salts, suspended solids, and water-soluble trace metals must be removed from crude oil. This reduces the corrosion, plugging, and fouling of equipment. It also prevents poisoning any of the catalysts in processing units.
Both chemical and electrostatic separation desalting involve the combination of hot water and additional chemicals to purify the oil. These chemicals include things like:
- Surfactants
- Ammonia
- Caustic
- Acid
Once added to hot crude oil, these chemicals help transfer salts and other impurities to the hot water.
Safety concerns of oil desalting
This process of desalting can cause potential safety issues:
- Fouling of heater tubes and heat exchangers throughout the refinery
- Equipment failures due to increased pressures and temperatures
- Fire due to a leak or release of crude oil from heaters
- Release of harmful low-boiling point components of crude oil
When elevated operating temperatures are used to desalt sour crude oils, hydrogen sulfide (H2s) will be present. Within the oil and gas industry, H2S is a major concern and one of the leading causes of workplace health issues.
Desalting can also expose workers to ammonia, dry chemical demulsifiers, caustics, and acids.
The way to protect against these hazards is to follow safe work practices and to use appropriate personal protective equipment (PPE). And that is the case for every stage of the process. Workers should have PPE whether they are sampling products, inspecting facilities, repairing equipment, and generally working around harmful chemicals.
Crude oil distillation (fractionation)
Once crude oil is cleaned, it is then separated into various fractions by distillation in both atmospheric and vacuum towers. These fractions have specific boiling-point ranges and volatilities.
Crude oil is fed into a heater and distillation column from temperatures of 650°F to 700°F. It separates into vapor and rises up the tower, where products of various densities are drawn off. Many facilities use steam to lower the vapor pressure and create a partial vacuum within the tower.
Safety concerns from oil fractionation
Even though these are closed processes, heaters and exchangers in the units could provide a source of ignition. If a leak occurs, the unit can catch fire and pose a risk of injury and explosion.
Multiple areas of the process are susceptible to corrosion from HCl, H2S, sulfur compounds, and organic acids. Sometimes, ammonia and alkaline solution are injected into steam or the hot crude oil feed. These chemicals may then be present at high wastewater concentrations, putting workers at risk for inhalation of hazardous materials.
If automatic control devices fail, the pressure and temperature of the oil may skyrocket. When this happens, distillation towers may crack and burst.
PSM in oil and gas should address how you will control temperature, pressure, and reflux to prevent thermal cracking within distillation towers. It should also ensure that relief systems are capable of relieving pressure and preventing crude oil from entering the reformer charge.
Solvent extraction and dewaxing
Since distillation separates petroleum products into groups only by their boiling-point ranges, impurities may remain.
Solvent refining processes usually remove these undesirables at intermediate refining stages or before sending the product to storage. The solvent extraction process separates impurities from the product stream through dissolvement or precipitation.
Dewaxing involves mixing feedstock with a solvent and cooling to dissolve and precipitate out wax and separate dewaxed oil. This typically involves the use of two solvents: toluene and methyl ethyl ketone.
Safety issues from solvent extraction and dewaxing
Because solvent extraction is a closed process, exposures are expected to be minimal under normal operating conditions. However, there is a potential for exposure to extraction solvents and other process chemicals. Although operating pressures are relatively low, fires are possible if leaks or spills occur and become ignited somehow.
Thermal cracking
Simple distillation of crude oil produces various amounts and types of products that are not consistent with those required by the marketplace. Oftentimes, the molecular structure of the product hydrocarbons must be changed for it to match industry standards.
The thermal cracking or catalytic cracking processes break heavy, high boiling-point petroleum fractions into products like:
- Gasoline
- Fuel oil
- Gas oils
This process takes place at high temperatures and pressure points. During this process, catalysts are added to the cracking reaction. This increases the yield of viable products. But like all other forms of oil refinement, thermal cracking also has potential safety issues.
Safety issues from thermal cracking
If contaminants enter the thermal cracking process stream, harmful gas and toxins may enter the atmosphere. You should regularly test the process inputs, products, and recycling streams for evidence of contamination.
Another major safety concern is severe burns. Thermal cracking happens at temperatures higher than 700 °F. If workers’ skin comes into contact with the scalding hydrocarbon liquids or vapors, they will suffer severe and extensive, possibly life-threatening, burns.
PSM in oil and gas operations helps to control these safety issues before incidents happen. To do this, you’ll need a process safety management system in place.
Process safety management systems
All process safety management systems should include:
- Process safety information
- Process hazard analysis
- Detailed standard operating procedures
- Mechanical integrity checks
- Extensive management of change (MOC) systems
All your operational plans and procedures should be up-to-date, complete, and accurate. They should provide clear instructions on specific steps for normal operations, non-routine or upset conditions, temporary operations, safe work practices, and emergency shutdowns.
Procedures should be performed as written. If operators deviate from procedures, management should address unsafe behaviors immediately. They should meet with operators to review the effectiveness of procedures and revise if necessary.
You should document all physical (e.g., fire, explosion) and chemical hazards and their effective controls. Make sure employees receive and have continual access to this information. If you find a hazard that has not been adequately addressed, you need to establish a system to mitigate the findings promptly.
Equipment deficiencies, such as lack of proper maintenance or repair, inappropriate installation, missing protective system (e.g., not including relief devices), and insufficient structural support, should be corrected immediately to avoid disastrous consequences.