Management of Change Form
Resources >Template Library > Management of Change Form
Download this free Management of Change Form from Frontline Data Solutions to document operational changes within your company.
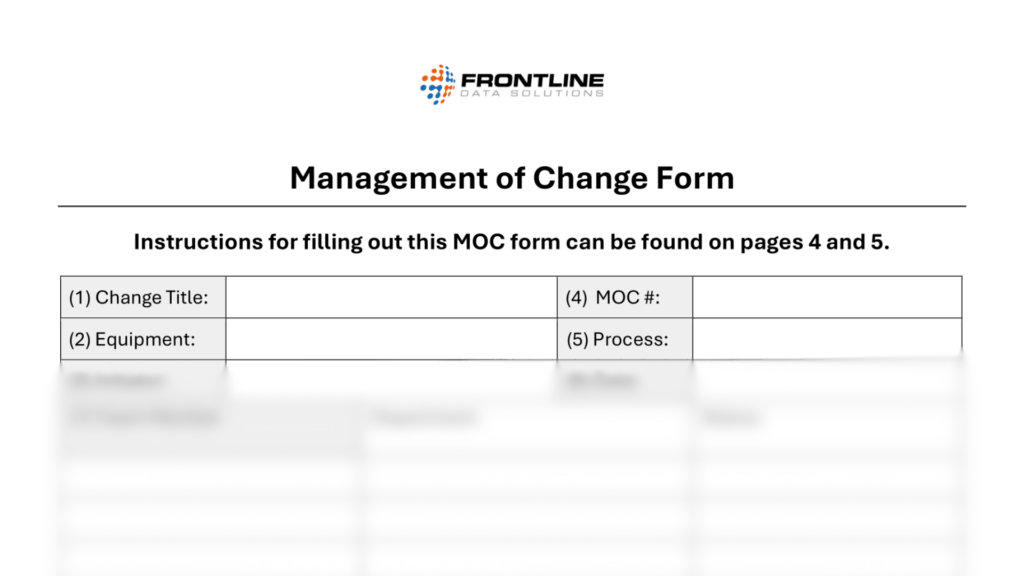
What Is a Management of Change Form?
A management of change form is a standardized document used to evaluate, approve, and track operational changes within your facility. It can help you identify potential hazards, assess risks, and implement safeguards before you make an operational change.
This form is a key part of a formal change management process, especially in industries where change can introduce new hazards—such as oil and gas, chemicals, manufacturing, or food and beverage.
Why You Need an MOC Form
Without an MOC form, critical steps can fall through the cracks—like reviewing hazards, notifying stakeholders, or updating procedures. Here’s why a formal form matters:
- It ensures consistency because your team follows the same steps for every change.
- It captures safety, environmental, and operational impacts before they cause issues.
- It supports compliance with OSHA’s PSM requirements and other regulatory standards.
- It maintains a documented history of changes, reviews, and approvals.
Even small changes—like swapping a chemical supplier or moving equipment—can trigger larger consequences. An MOC form gives your team the structure to think ahead and take preventive action.
What Should a Management of Change Form Include?
A well-designed MOC form should guide the user through each phase of the change management process. Here are the most important sections:
1. Change Description
Clearly define what the change is—equipment modification, process update, new material, etc.
2. Reason for the Change
Document why the change is necessary. Is it for safety, efficiency, cost savings, or compliance?
3. Scope and Impact Assessment
Evaluate what areas, processes, or people will be affected. Include potential risks and hazards.
4. Review and Approvals
Capture signoffs from key stakeholders—like safety, engineering, maintenance, and operations.
5. Pre-Startup Safety Review (PSSR)
Ensure all safeguards are in place before implementing the change.
6. Training and Communication
Identify if training or communication is needed for affected personnel.
7. Follow-Up Actions
Track any outstanding items, such as audits, documentation updates, or inspections.
8. Implementation Date and Status
Log when the change goes live and confirm that all requirements you’ve met all the requirements.
Example Use Case: Swapping Out a Valve
Let’s say your maintenance team wants to replace an old valve with a newer model. Without an MOC form, they might install it without considering whether:
- The new valve has the same pressure rating
- Operators need updated training
- Process safety information must be revised
- A new SOP is required
With a form, those checks become automatic—not afterthoughts.
Digitize Your Management of Change Form
While paper forms and spreadsheets are better than nothing, they often get lost, forgotten, or filled out inconsistently. That’s why many organizations are moving to digital MOC systems that automate workflows, ensure complete reviews, and centralize documentation.
Software like Frontline MOC provides built-in forms, customizable approval paths, and real-time status tracking—so nothing falls through the cracks.
If you’re building or improving your MOC process, download our Word template. It follows the requirements of OSHA’s PSM guidelines so your team has everything documented for compliance.
More Templates to Discover
Found this template helpful? You might like some of these, too: