The Japanese term “Andon” (アンドン) means “light” or “lamp,” and it comes from a manufacturing concept developed in the 1930s. Today, industries across the world use Andon systems to signal issues in the production process.
Sakichi Toyoda, one of the founders of the Toyota Motor Corporation, developed the lean manufacturing principles that many businesses use today. One key principle behind these systems is “Jidoka,” or “intelligent automation.”
Jidoka emphasizes quality control over productivity, and its primary goal is to reduce the number of defects that slip through the production process. At Toyota, employees apply the Jidoka concept by pulling an “Andon cord” to stop the car production line whenever they detect a problem.
If anyone pulls the cord, production halts immediately, directing all the managers’ attention towards fixing the problem. This allows the business to achieve long-term operational success rather than short-term productivity.
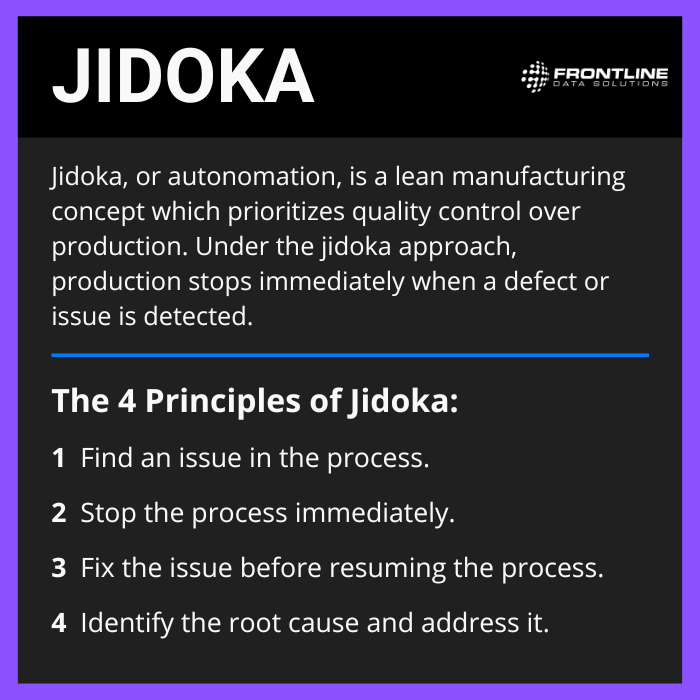
Implementing an Andon System
The biggest benefit of deploying an Andon system is that it teaches employees to be proactive when they notice problems in the process. Not only is this invaluable for maintaining product quality standards, but it also helps to create a strong safety culture.
Because jidoka is simply a methodology, how you choose to implement an Andon system is entirely up to you. And this will largely depend on the processes that you already use. However, regardless of industry, there are three main types of Andon systems: cords, lights, and boards.
Andon Cords
In the automotive industry, cords are the most common type of Andon system. You can think of Andon cords like the pull cords on a city bus. Just as passengers pull a cord to alert a bus driver to stop, workers use Andon cords to trigger a kill switch that halts production until someone resets it.
This is the original system that Toyota used to establish the Jidoka principles in its manufacturing facilities. And it holds true to the concept by ensuring that no production can take place when there is a known quality issue.
Andon Lights
A less disruptive but similarly effective approach is the use of Andon lights. Unlike cords, Andon lights don’t always affect the entire production line. Rather, they can signal problems at either individual workstations or a major operational component. These lights typically come in a stack with multiple color options, such as red, blue, yellow, and green.
In the example below, you’ll see that the Andon lights tower above pack stations so that managers can see them from far away if necessary:
Workers activate Andon lights by pressing a button, with each color corresponding to a different need.
In the warehouse setting, for example, a blue light often means that the worker needs a supply restock (boxes, tape, etc.) while a red Andon means they need immediate assistance in order to solve an issue.
These lights signal members of the leadership team to head over and fix the problem so the employee(s) can resume production. The benefit is that these lights don’t interrupt the larger operation if the issue is only minor.
Workers maintain control over the process and receive encouragement to address issues immediately. Overall, the light system is a good option for processes where individuals work separately and may have issues that won’t immediately impact the larger operation.
Andon Boards
Finally, the Andon board provides a shared visual alert across the operation and typically appears in common areas throughout the facility. The Andon board displays important operational information like:
- Quality defect rates (DPMO)
- Department productivity rates
- Production output
- Pending Andons
Modern Andon boards are television screens that update regularly to display the most recent operational data. They allow anyone within the operation to gauge critical information and guide managerial decisions throughout the workday.
Analyzing Data From Your Andon System
Using Andon systems allows you to collect otherwise unknown data about your operation. Here are just some examples of the types of information you can gather:
- Most common causes of Andons
- Frequency of Andon requests
- Distribution and concentration of Andon requests throughout the site
Depending on your setup, you may have to record this data manually. But if your Andon boards automatically track the data, you can easily access it for increased insight.
Another way to utilize your Andon systems for process improvement is to track action items for major Andons. So, if production shuts down to fix a process-wide issue, you can manage all resulting action items in the cloud.
Over time, you’ll create a database of information on the root causes of these problems, solutions that do and don’t work, the time and cost for each solution, etc. At least once a quarter, analyze this data and look for patterns. Determine new areas of opportunity and improvement projects that you can tackle going into the next quarter.
If you do this, you will have truly tapped into the benefits of the jidoka framework. And you’ll end up with a more efficient operation, a stronger safety culture, and a higher standard of product quality as well.