The global industrial revolution of the 17 and 1800s ushered in a new era of workplace safety policies in the 1900s. Seeing the dangers of manufacturing work, governments began collecting safety data and establishing regulatory agencies for enforcing factory safety rule standards. Today, factory safety rules govern how both leaders and workers take accountability for workplace safety and incident prevention.
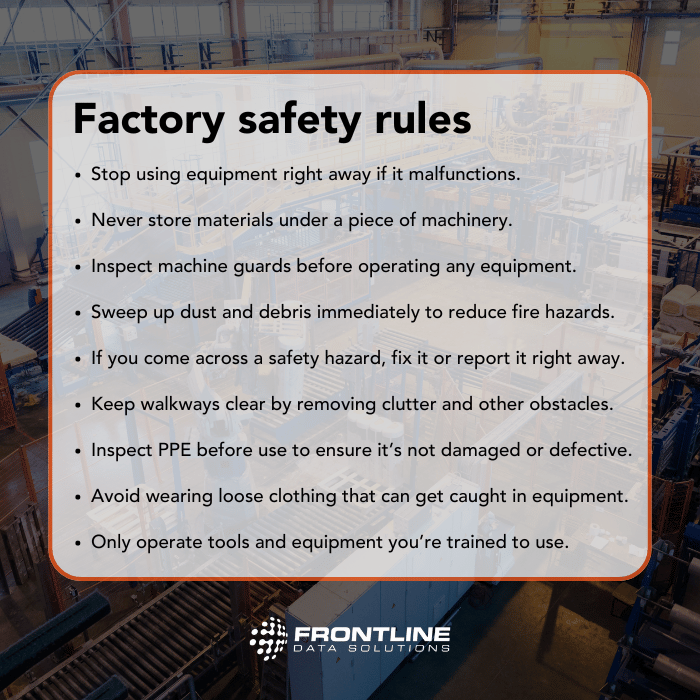
Factory Safety Rules for Workers
Getting workers to follow factory safety rules can be difficult, especially if you aren’t consistent. It takes consistent enforcement over a long period of time to create a strong safety culture. The less strict you are, the harder it will be to maintain a rule long-term.
Here are some common rules that manufacturing workers should follow to stay safe:
- Never leave your tools lying around where someone can get hurt because of them.
- Keep hair, nails, and clothing tidy and at the standard length.
- Ensure that emergency equipment (e-stops, fire extinguishers, etc.) is always accessible.
- Red tag broken or damaged equipment and set it aside until repaired or replaced.
- Follow the 5S layout for each area to eliminate fall hazards.
- Only operate tools and equipment you’re trained to use.
- Check that all energy-powered devices are locked out during repair or maintenance.
- Never attempt to repair equipment unless you’re certified to do so.
- Wear the required PPE for each task you perform.
- Inspect PPE before use to ensure it’s not damaged or defective.
- When using hazardous machinery, notify others in the area beforehand.
- If you come across a safety hazard, either fix it or report it right away.
- Keep your work area clean as you go to prevent slips, trips, and falls.
- Stop using the equipment right away if you notice any issues or malfunctions.
- Notify HR if your emergency contact information changes.
- Never store materials under a piece of machinery (conveyor belt, press, centrifuge, etc.).
- Keep all non-essential personal items off the factory floor.
- Report injuries and illnesses as early as possible to prevent them from getting worse.
- Inspect machine guards before operating any hazardous equipment or tools.
- Avoid wearing loose clothing that can get caught in manufacturing equipment.
- Eat food and drinks (besides water) off the factory floor so they don’t attract rodents.
- Sweep up dust and debris immediately to reduce fire and explosion hazards.
- Maintain clean and clear walkways by removing clutter and other obstacles.
Of course, your policies should be site-specific to the processes and equipment you have in place. The more relevant the rules, the easier it’ll be for employees to understand the “why” behind them.
Safety Rules for Leadership to Follow
Employee behavior is only one side of the equation. In fact, it’s possible that managers have even more rules to follow.
As a safety leader, it’s your responsibility to set an example for your team. But you also must ensure that the factory is safe in and of itself. This means setting standards for other areas of safety—maintenance, audits, documentation, etc.
Here are some rules you can establish for your leadership team to ensure that everyone’s setting the best example and contributing to the EHS program:
- Always practice the same safety behaviors you expect of your team while on the floor.
- Inspect the facility quarterly for structural damage, security concerns, etc.
- Never assume that employee behavior is the root cause of an incident—always look for other possibilities.
- Carefully track and manage any changes that could impact health and safety in the factory.
- Avoid cellphone use on the production floor unless it’s essential.
- Keep laptops, radios, and other equipment out of the way of people, equipment, and processes.
- Conduct regular job hazard analyses to stay on top of preventative safety measures.
- Give workers advance notice of changes to equipment, policies, processes, etc.
- Solicit feedback before implementing a change across your entire facility.
- Ensure a consistent stock of safety materials like first aid supplies, PPE, and more.
- When a safety incident happens, use it as a learning opportunity for your whole team.
- Investigate all near misses and follow up to prevent them from happening again.
- Retrain any employees involved in a near miss or incident within a week.
- Keep detailed records of training, including onboarding, refreshers, and ad hoc sessions.
- Never rush an employee through the training process, especially if they’re not confident yet.
- Allow floor managers enough time each week to engage with the workforce.
- Do an annual review of all training materials to make sure they’re accurate and updated.
- Follow up with hazard reports immediately to assess the risk level and make corrections.
- Apply the same safety policies to both managers and frontline workers.
- Check contractor documentation monthly to ensure all permits are up to date.
Documenting Your Program
The better your team’s documentation, the easier it’ll be to maintain compliance and implement effective control measures. With an action tracking system, you can centralize the data so it’s accessible to anyone at any time. This means that executive leaders can stay on top of safety performance and your EHS team can focus on making actionable improvements.
But even if you don’t have a software system, a basic spreadsheet can work as well. The main thing is that you improve recordkeeping habits so you can learn from your strategies and come up with new ones. Long-term, this will help you write even more effective factory safety rules for your team to follow.
For comprehensive information on OSHA regulations and guidelines, you can visit the official OSHA website at www.osha.gov.