Improving PIT training at your site
According to the 2021 Training Industry Report, the biggest training challenge during the COVID-19 pandemic was getting workers engaged in remote training. The second-biggest challenge was a lack of resources and personnel to complete classes.
While inconvenient, these are relatively manageable issues in traditional training environments. But for those whose workers need PIT training for things like forklifts, order pickers, and reach trucks, common approaches to improved efficiency might not work.
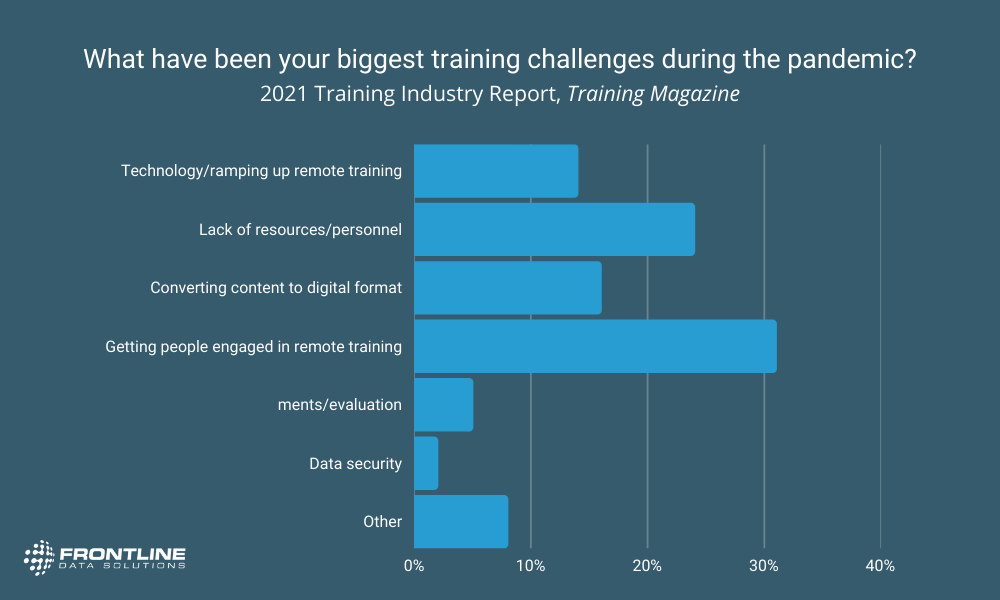
Ineffective PIT instruction
A common problem that you might come across is a lack of engagement among your students. Some of this is due to the training environment and some of it’s due to the training materials themselves.
Instructors either can’t or don’t always factor in different learning styles. So, while some students benefit from PowerPoint presentations and verbal explanations, others get lost. This creates a gap in the students’ ability to complete their PIT practicals on time.
Aside from trainees’ limitations, here are some of the other PIT safety training issues you might have to deal with:
- Not enough equipment to train multiple workers at a time
- No established schedule for training classes
- Unideal ratio of students to instructors
- Limited instruction space that creates bottlenecks for completing PIT practicals
You might not be able to control all these variables. Not all sites have the same resources and it’s unrealistic to expect that each PIT driving class will go to plan. Still, proper planning and better organization can completely transform how efficiently your team completes training.
Keeping PIT operators engaged
A 2019 study published in Proceedings of the National Academy of Sciences (PNAS) found that there are three main factors that help students remember a piece of information:
- How much time passes between first hearing it and hearing it again.
- How many times they review it.
- The total amount of time that they hear it repeated.
You can apply this insight to your own training sessions. By keeping students engaged, even when they’re not driving, you increase their retention of important PIT safety information. One way to do this is to have a “call and response” approach to certain key pieces of information.
Imagine, for example, that you’re helping one student practice driving. Meanwhile, other students are waiting for their turn. During this downtime, you can intermittently ask them questions related to the classroom training they received.
Doing this as a group exercise, rather than in an individual setting, may increase the engagement level. And students benefit from a higher-energy training experience.
Another thing you can do to increase retention is to have regular check-ins with new operators. During these check-ins, make sure operators have all the knowledge and skills they need to continue driving safely. The other added benefit of this approach is that it builds trust between the workers and the safety team.
As you make your training more engaging—and therefore, more effective—you should also look at improving it on the back end. For many sites, the amount of paperwork needed to document a PIT training class slows down the safety team and detracts from other important tasks.
Inefficient reporting systems
Although convenient for some, a paper approach to OSHA recordkeeping slows down many teams. Take a PIT warehouse training class as an example.
Imagine you have new employees in a corral learning how to drive an order picker. While students are driving, you have to devote your full attention to the instruction. This means that you have to fill out training documents after the session ends.
While this instruction is happening, you might have other students sitting on the sidelines. In most cases, those students are stuck waiting for their turn. If you have reports to fill out in between sessions, the process takes even longer.
Even if you fill out reports after you finish PIT training sessions, you probably still have to upload them to a digital system of some sort. This adds time to the work day. And until you finish your evaluations, none of the workers can drive PIT equipment.
None of this even factors in the classroom instruction that takes place before practical driving lessons. So, lessons which start in the classroom now take days to complete. For each day over the estimated training time, overhead expenses increase while output stays the same. With larger class sizes, the impact is even greater. But all of this cost can be avoided with a more efficient system for documenting PIT training.
Learning management systems for PIT training
To eliminate as much paperwork as possible, companies can adopt a learning management system (LMS). An LMS takes away some of the burden of conducting classroom training. It does this by allowing students to complete certain training modules on their own, instead of with an instructor.
With LMS software you can:
- Let students complete general training ahead of PIT driving instruction.
- Track training completion for new hires.
- Pull custom training records for individuals or groups.
- Save time by having students complete online assessments.
- Decrease the amount of time it takes for an instructors to fully document all the training they’ve completed for a class.
- Create custom report workflows for PIT trainers.
- Store all training documents in a central location.
- Set up notifications that remind trainers to complete evaluations promptly.
This type of digital management system is most effective when you fully integrate it with your standard work. Getting rid of paper records (where possible) means less redundancy. And you’ll be better equipped to track when operators need to renew their licenses for compliance reasons.
This leaves you with more time to interact with new PIT operators after they’ve hit the floor. With this combination of improved engagement and a more streamlined reporting system, your PIT training will become more efficient. And this opens the door for you to address other areas of not just your equipment training, but other areas of the operation as well.