CASE STUDY
SeAH Steel Replaces Manual Tracking Methods with Frontline ACT
After replacing their manual processes with Frontline ACT, the EHS team at SeAH Steel has regained precious time and boosted performance.
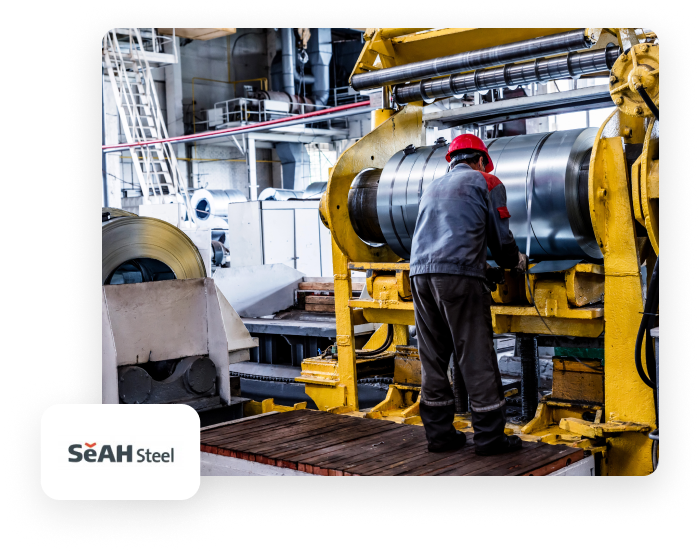
Meet SeAH Steel
Since its establishment in 1960, SeAH Steel has specialized in steel materials used in various industries, including energy, automotive, heavy machinery, shipbuilding, and construction.
SeAH excels in producing pipe and tube that meets the demands of the harshest environments, including those with extreme temperatures and highly corrosive conditions.
Industry: Mining
Company Size: 200+ employees
Challenges: Spending too much time manually tracking EHS program
Solutions: Frontline ACT
Inefficient and Ineffective Paper and Pen System
SeAH Steel has spent the past 50+ years perfecting its mining and processing of high-quality steel materials. So, it makes sense that they wanted to find ways to improve their behind-the-scenes operations as well.
One specific area they wanted to tackle was their EHS tracking and reporting approach. Employees manually documented and tracked safety action items using paper forms and spreadsheets. But as the business grew, the EHS team outgrew their manual processes.
As anyone using a pen and paper approach knows, this can leave a lot of room for errors and oversights. From constantly having to restore files or meet in person to discuss progress, it’s really hard to sustain this system long-term.
These, and other issues, caused SeAH Steel to explore alternative methods of action tracking.
Accurate and Organized EHS Data
The team at SeAH Steel wanted a system that could handle all their EHS data. And they wanted something to prevent workers from updating data over each other, causing inaccuracies.
Our action tracking system, Frontline ACT, solved both of these problems and more. Because it provides regular data backups and cloud-based storage, SeAH Steel doesn’t have to worry about working with outdated information.
As soon as someone updates an action item, attachment, etc., the system automatically updates the available records. And because entering and updating records is so easy to do (even from day one), this allowed SeAH Steel to get up and running quickly.
Frontline ACT also eliminated the EHS team’s monthly, 2-hour long meeting to review action items. Now, system administrators can pull progress records in minutes. With all the time they’ve saved, the EHS team can focus on implementing effective control measures and other improvement projects.
“Having a central, safe location for all our events and action items to be accessed, and tracked, has improved productivity and saved us many hours.”
Tracie Holler, HSE Coordinator
Frontline ACT Keeps Track So You Can Stay on Track
From the first day you implement our action tracking system, you’ll be able to assign and track tasks for things like incident investigations, improvement projects, and more.