We talked to Davenj Bradley, GSP, about the challenges of identifying risks in highly hazardous work environments. This interview explores the basics of hazard assessment, as well as key strategies for risk identification and mitigation.
About Davenj Bradley
Davenj Bradley is a Regional Environmental, Health, and Safety (EHS) professional with extensive experience in risk management, sustainability, and engineering. He has worked extensively in various industries, focusing on implementing sustainable and effective safety solutions crucial for risk identification and mitigation.
Davenj’s journey in EHS began with a passion for sustainability, workplace safety, and risk mitigation. With an educational background in engineering and sustainability, he was drawn to the EHS field as a way to integrate these disciplines and protect workers, optimize processes, and ensure regulatory compliance. Furthermore, his experiences to date include time in manufacturing, construction, and e-commerce logistics. Over the years, he’s successfully developed and implemented risk assessment strategies in a variety of environments, making risk identification and mitigation a priority.
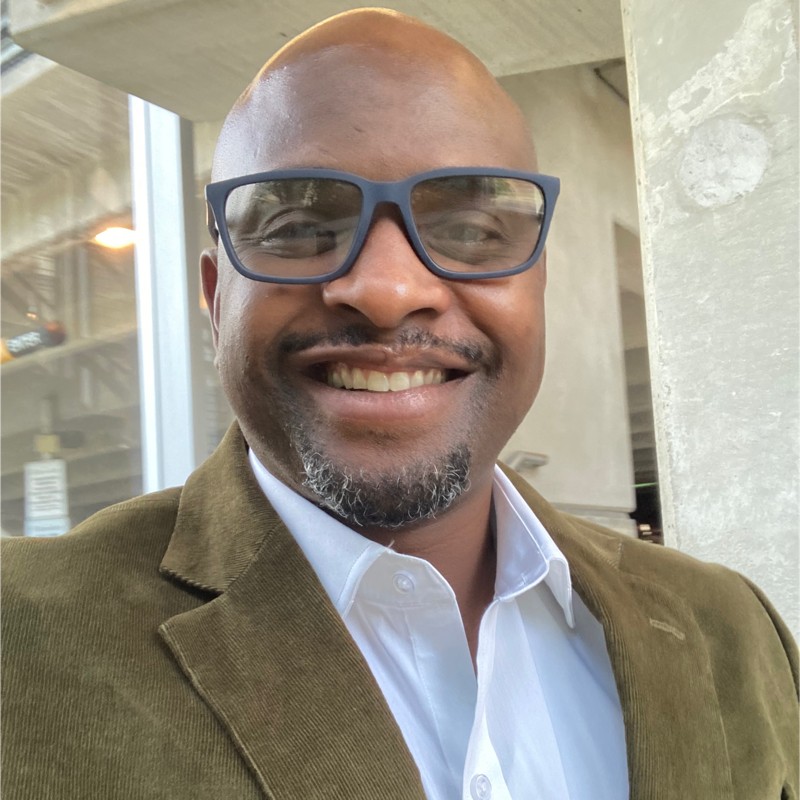
Risk Identification and Mitigation
Throughout his career, Davenj has conducted comprehensive risk assessments, implemented control measures, and established sustainable safety programs. His expertise includes hazard analysis, compliance auditing, and continuous improvement strategies to effectively manage risk identification and mitigation.
He’s also worked closely with cross-functional teams to develop proactive safety measures that align with both regulatory requirements and corporate sustainability goals.
1. In your experience, what are some of the hidden sources of risk that teams might not be aware of in their facilities?
Hidden risks often include poor ergonomic setups, improper storage of hazardous materials, overlooked electrical hazards, and process deviations that seem minor but can lead to major incidents. I’ve also found that organizational culture and lack of employee engagement can create latent risks that you can’t immediately see but they significantly impact safety.
2. What is your typical process for doing a risk assessment? Do you have a specific framework or set of steps that you use?
I adhere to a systematic risk assessment with several key steps. First, I identify hazards by conducting workplace observations, reviewing incident reports, and engaging with employees to gather their insights. My next step is do a thorough risk analysis, evaluating both the likelihood and severity of the identified hazards.
After this, I usually prioritize the risks through a risk evaluation, considering their potential impact and the level of exposure. To mitigate these risks, I implement a range of control measures, including engineering, administrative, and personal protective equipment (PPE) strategies.
The last step to any risk assessment is testing the effectiveness of your control measures. I usually do this by conducting periodic audits and making adjustments based on the results.
3. What’s the best way to handle operations leaders or frontline workers who disagree with the EHS team on the risk of a certain process, tool, etc.? Do you have any advice for effectively communicating why you’ve identified something as a potential risk?
Certainly, open communication is the key to navigating disagreements. I present data and real-world examples to clearly illustrate potential risks. Remember, you want the discussion to be grounded in factual information. Your strategy for risk identification and mitigation is only as strong as the effectiveness of your controls.
I’ve found that if you engage your workers in risk assessments and the decision-making process, it empowers them to voice their perspectives. I tend to offer alternative solutions that not only align with operational goals but also uphold safety standards. I also rely heavily on storytelling and case studies to emphasize the importance of addressing risks. People are more likely to get onboard with a policy or a change if they understand the real-world consequences of inaction.
4. How should EHS teams prioritize risks after they’ve identified them?
I use a risk matrix approach that categorizes risks based on severity and probability. High-severity and high-likelihood risks take top priority, followed by those with lower severity but higher probability. You have to align your risk prioritization criteria with the goals of your team and your business.
5. How do you distinguish between acceptable and unacceptable risks in a facility?
To me acceptable risks are the ones that we have controlled to the lowest possible level, that meet compliance standards, and that do not pose an imminent threat to workers or operations. Unacceptable risks are ones that have the potential to cause serious harm, violate legal requirements, or significantly disrupt the operation.
6. Do you think there’s a tendency to rely too much on behavioral safety and employee training as a risk mitigation strategy? If so, what should companies focus on instead?
Yes, while behavioral safety and training are critical, they shouldn’t be your sole mitigation strategy. You need to focus on engineering controls, process improvements, and hazard elimination at the source. When you do emphasize training as a control strategy, make sure it’s interactive, scenario-based, and regularly reinforced for the best results.
7. In your opinion, what is the key to ensuring that safety controls remain effective over time?
I’d say that regular audits, employee feedback loops, and leadership engagement are the main ingredients to a successful risk identification and mitigation strategy. Implementing leading and lagging indicators helps track control effectiveness, while periodic retraining and technology integration (such as IoT sensors for hazard detection) enhance long-term safety performance.
8. What’s your best advice for any EHS professional who’s feeling overwhelmed by the number or degree of risks they need to deal with?
All things considered, prioritize, delegate, and leverage technology. Not every risk requires immediate resolution—focus on high-impact hazards first. Build strong relationships with leadership and workers to foster a safety culture. Continuous learning and collaboration with peers in the industry can also provide valuable insights and solutions.
Davenj’s EHS Resources
Aside from his thoughts on risk identification and mitigation, we asked Davenj to share some of his top EHS resources for staying up to date and informed. Check out his recommendations below!
Favorite EHS Organizations
Davenj is a big fan of getting involved in the EHS community. His two favorite organizations to network with are the National Safety Council (NSC) and the American Society of Safety Professionals (ASSP). He also recommends staying updated with OSHA’s updates and peer-reviewed journals.
Davenj’s Best Advice for EHS Professionals
When asked what the best advice he’s ever received in the EHS field was, Davenj said:
“Safety is not just about compliance; it’s about fostering a culture where everyone feels accountable for their own well-being and that of their colleagues.”
“This transformative mindset shifts EHS from merely being a set of rules to becoming a core organizational value that promotes continuous improvement and innovation. It’s crucial to remember that [EHS professionals] are in the prevention business, and without our people, opportunities to improve safety outcomes are limited. This principle has led me to embrace and live by a powerful mantra: “I MATTER, YOU MATTER, WE ALL MATTER!”